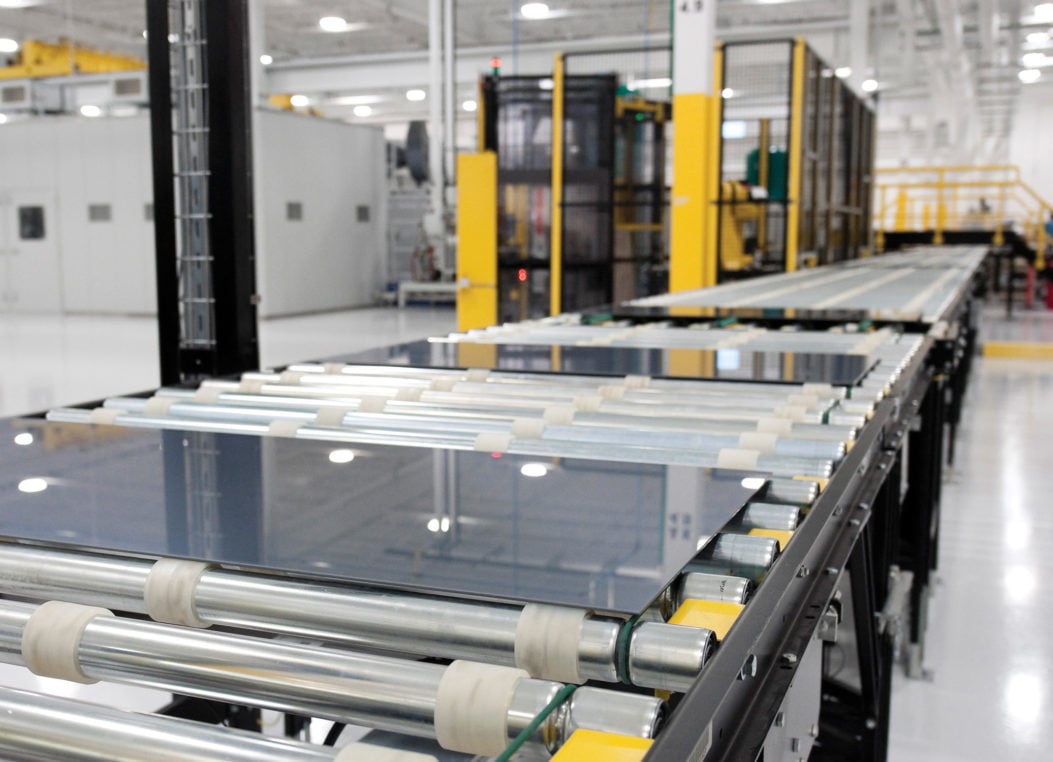
Thin-film funding
By far the largest beneficiary of funds is Cadmium Telluride (CdTe) thin-film solar manufacturer First Solar, which bagged US$21 million in two separate investments of US$15 million and US$6 million for its facilities in Ohio and Arizona.
Thin-film solar firms generally received a higher proportion of investment than silicon-based companies. The DOE said that it identified CdTe technology in particular as “an opportunity to expand domestic production of solar panels” in its Solar Photovoltaics Supply Chain Review.
Indeed, CdTe has become the dominant commercial thin-film product in the solar industry and is uniquely isolated from the global silicon supply chain that ties silicon-based solar manufacturers to production sites in China. Trade tensions between the US and China have been mounting of late.
Next-generation tandem solar companies also secured funding, notably perovskite solar companies CubicPV and Swift Solar, which received US$6 million and US$7 million respectively.
The full list of thin-film projects to receive funding is as follows:
- First Solar (Tempe, AZ and Perrysburg, OH): US$15 million
- Swift Solar (San Carlos, CA): US$7 million
- Cubic PV (Bedford, MA): US$6 million
- First Solar (Tempe, AZ and Perrysburg, OH): US$6 million
- Tandem PV (San Jose, CA): US$4.7 million
- Tau Science (Redwood City, CA): US$2.1 million
- 5N Plus (Montreal, Canada): US$1.6 million
- Brightspot Automation (Boulder, CO): US$1.6 million
The DOE said that of these eight projects, four will develop efficiencies and resilience for CdTe systems and four will focus on tandem thin-film products like perovskite and copper indium gallium diselenide (CIGS).
The DOE said that the investment package advances the Biden administration’s Justice40 Initiative, which seeks to ensure that 40% of “overall benefits” from federal climate investments go to disadvantaged communities.
Silicon support
The DOE also selected three projects to bring silicon wafer and cell manufacturing to the US. This includes South Carolina-based solar manufacturing Silfab, which is building a 1GW solar cell facility to produce n-type tunnel oxide passivated contact (TOPCon) cells.
Wafer production has so far failed to benefit from the manufacturing incentives introduced under the Inflation Reduction Act (IRA) to the same extent as cell and particularly module production. So far, the only confirmed, large-scale wafer production is being developed in the state of Georgia by Korean-owned solar manufacturer Qcells.
Last week, PV Tech Premium looked at the potential for the US to onshore wafer and polysilicon production capacity, and the challenges that it faces if it is to realise this potential.
The DOE said that the investments would “support the development of technologies” to bring wafer and cell capacity onshore, and “enable new solar companies to prove out their technologies with the goal of becoming eligible to apply for capital to scale-up manufacturing, accelerating their path to commercialisation.”
The remaining seven recipients are engaged in dual-use PV products, such as building-integrated PV (BIPV) and deploying in the transport sector.
The full list of silicon-based recipients is as follows:
- Ubiquity Solar (Hazelwood, MO): US$11.2 million
- Silfab Solar Cells (Fort Mill, SC): US$5 million
- Re:Build Manufacturing (Nashua, NH): US$1.9 million
- Appalachian Renewable Power (Stewart, OH): US$1.6 million
- GAF Energy (San Jose, CA): US$1.6 million
- Noria Energy Holdings (Sausalito, CA): US$1.6 million
- Wabash (Lafayette, IN): US$1.6 million
- The R&D Lab (Petaluma, CA): US$1 million
- RCAM Technologies (Boulder, CO): US$600,000
- Silfab Solar WA (Bellingham, WA): US$400,000